top of page
Publications

Design Analysis of a Fabric Based Lightweight Robotic Gripper
The development of grasping mechanisms for various grasping applications have enabled robots to perform a wide variety of tasks in both industrial as well as domestic applications. Soft robotic grippers have been very useful in grasping applications with an added advantage of simpler control mechanisms as compared to rigid grippers. In this paper, a two fingered gripper inspired by the fingers of a human hand is introduced. The gripper is made from fabrics and, hence, compliant, lightweight, completely foldable and boasts a high payload capability. The mechanical design of the gripper is optimized through experiments, a maximum bending angle of 180° is achieved. We demonstrate grasping of a variety of objects using the new gripper.

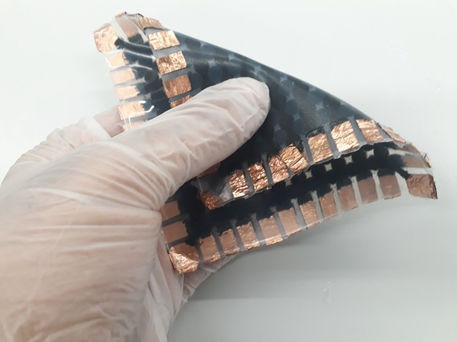
Modelling of a Soft Sensor for Exteroception and Proprioception in a Pneumatically Actuated Soft Robot
Soft sensors are crucial to enable feedback in soft robots. Soft capacitive sensing is a reliable technology that can be embedded into soft pneumatic robots for obtaining proprioceptive and exteroceptive feedback. In this paper, we model a soft capacitive sensor that measures both the actuated state as well as applied external forces. We develop a Finite Element Model using a multiphysics software (COMSOL®). Using this model, we investigate the change in capacitance with the application of external force, for a range of different internal pressures and strains. We hope this study is helpful in understanding the coupling of internal inputs and external stimuli on the feedback obtained from the sensors and help us design better sensory systems for soft robots.


Light Intensity-Modulated Bending Sensor Fabrication and Performance Test for Shape Sensing
Notable advancements in shape sensing for flexible continuum robot arms can be observed. With a keen interest to develop surgical and diagnostic tools that can advance further and further into inaccessible spaces along tortuous pathways, such as the human body, a need for the precise determination of the robot’s pose arises. Whilst there have been techniques developed that use external sensors to observe the advancing robot from the outside to determine its location and orientation in space, there is an observable trend towards using integrated, internal sensors to measure these positional parameters. Especially in the medical world with its tough requirements on robot size, e.g., catheter-type robots, most pose-sensing approaches to date make use of a technique called Fiber Bragg Grating (FBG). FBG sensors make use of fibers that are grated, and the amount of bending can be determined with an appropriate optical interrogator. Although these fiber sensors have been successfully employed to measure the deformation and through advanced signal processing the pose of continuum catheters, they have a major drawback which is their exorbitant cost. To address this issue a different design and fabrication process is proposed to produce an affordable shape sensor that is highly flexible and can detect bending. The method of operation involves a segmented flexible robot arm with three waveguides in a 120-degrees configuration. The segments are made of silicone elastomer with channels that encapsulate light propagating internally, with a photodiode and light-emitting diode (LED) embedded in each individual channel. The prototype was developed and characterized for strain, and bending response detection.

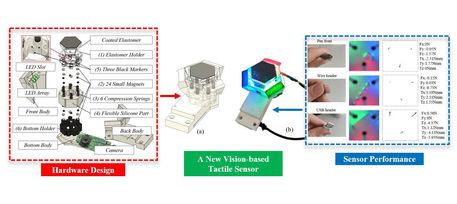
F-TOUCH Sensor: Concurrent Geometry Perception and Multi-Axis Force Measurement
Force and tactile sensing has experienced a surge of interest over recent decades. It conveys a range of information through physical interaction, including force, pressure, texture and vibration. Even so, existing tactile sensors have difficulty in precisely acquiring force signals to capture magnitude and direction. This is because vision-based tactile sensors, such as the popular GelSight sensor, estimate force and torque from discrete markers embedded in a compliant sensor interface and detected via image processing, resulting in force errors that are sizeable. This paper presents a novel design for a force/tactile sensor, namely F-TOUCH (Force and Tactile Optically Unified Coherent Haptics), that signifies an appreciable advance on current state-of-the-art tactile sensors. In addition to the acquisition of geometric features via the (silicone) elastomeric component at a high spatial resolution, our sensor incorporates a deformable spring-mechanism structure, allowing us to measure translational and rotational force and torque along six axes with high accuracy. The proposed sensor contains three principal components: a coated elastomer layer acting as the compliant sensing medium, spring mechanisms acting as deformable structural elements, and a camera for image capture. The camera records the deformation of the structural elements as well as the distortion of the compliant sensing medium, concurrently acquiring force and tactile information. The sensor is calibrated with the aid of a commercial ATI Industrial Automation ® 6-axis force/torque sensor. An experimental study reveals that the F-TOUCH sensor outperforms GelSight as a force sensor.

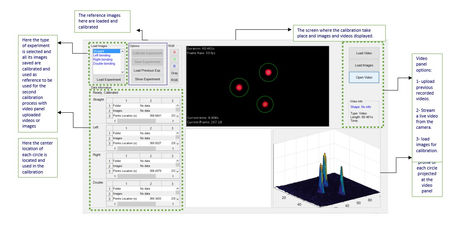
Towards Creating a Flexible Shape Senor for Soft Robots
Recent advances in robotics have witnessed an increasing transition from designing conventional robots with rigid components to partially or completely soft ones. Soft robots are known to be highly deformable and stretchable which makes the process of registering their shape and orientation in 3D challenging. This paper presents a first step of creating a flexible shape sensor for soft robots and a calibration algorithm that can compensate for different planar deflection conditions. In this paper, we describe the design and fabrication of the proposed shape sensor prototype utilizing three segmented optical fibers along the length of a flexible continuum arm. Three experimental scenarios of deflection are investigated to validate the relation between a mechanical deflection of the prototype and the change in intensity of the optical fibers' tip outputs (15 degrees deflection to the right and left, and planar double-bending). Camera images of the intensity circles without bending are used as a reference to relate the images features (location, angles, size, and intensity) to other bending cases. This study demonstrates the potential of relating the deflection status of a soft sensor to the image samples collected through a camera for the purpose of reconstructing and calibrating the shape sensor in 2D-space using MATLAB image processing toolbox and machine learning.

EPAM: Eversive Pneumatic Artificial Muscle
Pneumatic Artificial Muscles, which are lightweight actuators with inherently compliant behavior, are broadly recognized as safe actuators for devices that assist or interact with humans. This paper presents the design and implementation of a soft pneumatic muscle based on the eversion principle - Eversive Pneumatic Artificial Muscle (EPAM). The proposed pneumatic muscle exerts a pulling force when elongating based on the eversion (growing) principle. It is capable of extending its length by a minimum of 100% when fully inflated. In contrast to other soft pneumatic actuators, such as the McKibben's muscle, which contract when pressurized, our EPAM extends when pressure is increased. Additionally, important advantages of employing the eversion principle are the capability to achieve high pulling forces and an efficient force to pressure ratio. In a pivoting joint/link mechanism configuration the proposed muscle provides motion comparable to human arm flexion and extension. In this work, we present the design of the proposed EPAM, study its behavior, and evaluate its displacement capability and generated forces in an agonistic and antagonistic joint/link arrangement. The developed EPAM prototype with a diameter of 25 mm and a length of 250 mm shows promising results, capable of exerting 10 N force when pressurized up to 62 KPa.


Virtual Reality Simulator for Medical Auscultation Training
According to the Oxford English dictionary, auscultation is “the action of listening to sounds from the heart, lungs, or other organs, typically with a stethoscope, as a part of medical diagnosis.” In this work, we describe a medical simulator that includes audio, visual, pseudo-haptic, and spatial elements for training medical students in auscultation. In our training simulator, the user is fully immersed in a virtual reality (VR) environment. A typical hospital bedside scenario
was recreated, and the users can see their own body and the patient to increase immersion. External tracking devices are used to acquire the user’s movements and map them into the VR environment. The main idea behind this work is for the user to associate the heart and lung sounds, as heard through the stethoscope with
the corresponding health-related problems. Several sound parameters including the volume, give information about the type and severity of the disease. Our simulator can reproduce sounds belonging to the heart and lungs. Through the proposed VR-based training, the medical student ideally will learn to relate soundsto illnessesin a realistic setting, accelerating the learning process.
was recreated, and the users can see their own body and the patient to increase immersion. External tracking devices are used to acquire the user’s movements and map them into the VR environment. The main idea behind this work is for the user to associate the heart and lung sounds, as heard through the stethoscope with
the corresponding health-related problems. Several sound parameters including the volume, give information about the type and severity of the disease. Our simulator can reproduce sounds belonging to the heart and lungs. Through the proposed VR-based training, the medical student ideally will learn to relate soundsto illnessesin a realistic setting, accelerating the learning process.

A bending sensor insensitive to pressure: soft proprioception based on abraded optical fibres
Optical sensors have recently been proposed for sensing bending, linear strains and external forces in soft actuators. However, the susceptibility of these sensors to a number of stimuli makes it difficult to comprehend the resulting data output. We address this challenge through the introduction of a low-cost flexible bending sensor based upon the abrasion of optical channels. Such sensors are responsive to bending while being insensitive to internal pressure or external forces. The developed sensor is integrated into a soft pneumatic finger in order to obtain feedback of its curvature. We further demonstrate that the sensor is insensitive to normal forces
applied on a blocked finger. Through this work, we propose a simple, low-cost sensor development technique towards addressing the challenge of decoupling forces and deformations in soft robots.
applied on a blocked finger. Through this work, we propose a simple, low-cost sensor development technique towards addressing the challenge of decoupling forces and deformations in soft robots.
bottom of page